Membrane Roof Failure Risks Not Being Taken Seriously
- December 9, 2022
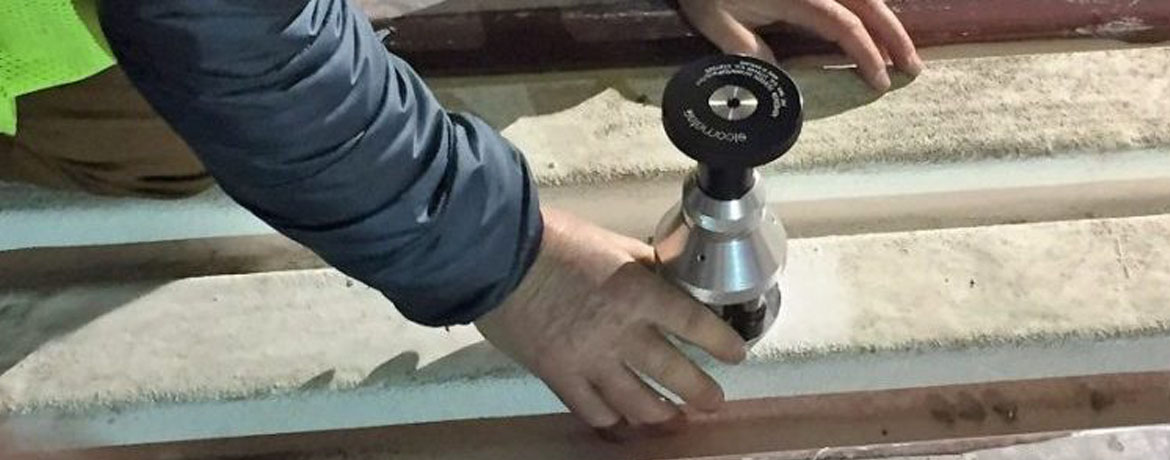
“Aotearoa – Six months in a leaky boat.”
There is some irony that at least Split Enz knew that they were in a leaky boat. So, in true kiwi stoic fashion, they celebrated it with a song. However, in the last six months, NZ has experienced weather events well beyond the expectation of the NZ Building Code. But that’s ok, right? Because over the past 20 years, we have become experts in weathertight buildings. Designing, inspecting and testing to ensure they don’t leak. Or have we?
External waterproofing is essential to a building’s life and success; vertical construction is only achievable when there is certainty in managing surface water from all external surfaces.
‘Flat membrane roofs, balconies & podiums’, through the fundamentals of their design, are arguably the most challenging external waterproofing system for successful water management. These horizontal surfaces have liquid or sheet membranes, torched, glued, and fixed to them, with a level of skill and experience that is nothing short of brilliance.
The installation of membrane waterproofing is a critical path item on a high percentage of NZ construction projects; now, with the rapid transition to Medium Density Housing and the increased height in residential structures, it is likely to become even more prominent.
So, what’s the problem?
For years BCA inspectors have become experts at checking substrates for membrane application and the sighting of completed works. That is truly commendable. However, it is not when the most significant membrane surfaces risk occurs.
After the completion of the membrane, the surface will instantly become the workbench for a carnival of proceeding trades, material storage, impromptu- smoko locations, etc. Let’s face it, an empty deck area (in a sunny spot) is just crying out to be used (AND ABUSED).
Smart builders protect the membrane, but who can honestly say they have never dropped a tool or even been aware of the screw lodged in their boot?
In short, the post-membrane completion construction phase is the most significant risk for the waterproofing membrane. And guess what? Nobody is coming back to check it is still watertight.
Alarming Evidence!
Test data for Electrical Membrane Testing was recorded over a 40-month period.
(855 Tests over 261 projects for new membrane installations)
Frankly, the results are alarming and merit serious industry concern!
– 74.6% of tests reported water tightness breaches (638 of 855)
– 2255 Watertightness Breaches were identified over a surface area of 137,000m2 of Roof & Podium Membrane
– 1 in 2 Balconies tested were found to have a watertightness defect (with a sample size of 1323 balconies)
Additionally, Non-Watertightness Areas of Concern were reported in 90.4% of the reports. (773 of 855) i.e., Mechanical damage, termination issues, Unfinished details, unsealed fixings penetrating membrane.
What is good practice?
There is a silver bullet to mitigate the damage left behind – External Waterproofing surfaces can be tested; ideally, this should be as late as possible before the building’s practical completion date.
There are two internationally recognised standards for testing & reporting the verification of the waterproofing watertightness for membrane roofs.
– ASTM 5958 – 98 (Reapproved 2005) Standard Guide for Flood Testing Horizontal Waterproofing Installations
And
– ASTM 7877 Electronic Methods for Detecting and Locating Leaks in Waterproofing Membranes
The Bad News
There is guidance from the Waterproofing Membrane Association Inc (The Torch On- Code of Practice), but Industry has had limited take up for mandatory testing.
Despite these test standards providing BCA’s reliable compliance evidence, very few BCA’s require membrane tests pre-CCC.
Many NZ manufacturers & suppliers require testing to confirm compliance in support of their warranty. However, there is no current guidance around when the testing should be carried out and for the majority of warranties the tests are not being completed.
One of the reasons that there is a reluctance to test is that it can be costly and impractical. Flood tests require the entire membrane surface area to be flooded to a 50mm – 100mm above the highest point. That equates to 1 tonne of water for every 10m² of the roof. That’s a lot of weight and indeed not to be undertaken without structural advice on temporary support. Also, don’t forget that you need to get rid of the water afterwards.
Electrical Leak Detection methods as described in ASTM 7877, are far simpler and cost-effective method.
Conductance Leak Location
The principle of the electronic leak testing method is the establishment of an electrical potential between the electrically insulating waterproof membrane and the conductive underlying substrate.
Electric conductance leak location requires that the substrate material directly below the membrane be sufficiently conductive for the test method employed. In most instances, a concrete substrate is sufficiently conductive to allow this method. In certain membrane assemblies, where the substrate is nonconductive, it is possible to install a conductive material directly under the membrane to facilitate testing.
Low Voltage Methods (Electric Field Vector Mapping EFVM®)
When testing using a low voltage electrical potential, a thin controlled covering of water on the surface forms the conductive path horizontally across the membrane to any membrane breach. At a breach location, an electrical path to the substrate is formed through the water connecting to the substrate below. A sensitive receiver detects the leakage current and alerts the operator to the exact location of this connection.
Ultimately, if leaks in membranes do go undetected, it may take more than six months to find you have a leaky boat, but when leaks are finally detected, as the song says, “Ship-wrecked love can be cruel.” And the money saved from testing will be trivial compared to repair cost.
Our recommendation is that Industry wakes up to the risk and insists on waterproofing membrane testing to ensure homeowners can remain confident that their properties are safe and compliant.
Written by Rob Tierney (Farsight NZ) and Thomas McLaughlin (ILD NZ)
Disclaimer: This publication is general in nature and should not be used as a substitute for legal or other professional advice. Please seek specific professional advice before acting in relation to any statement contained in this publication.